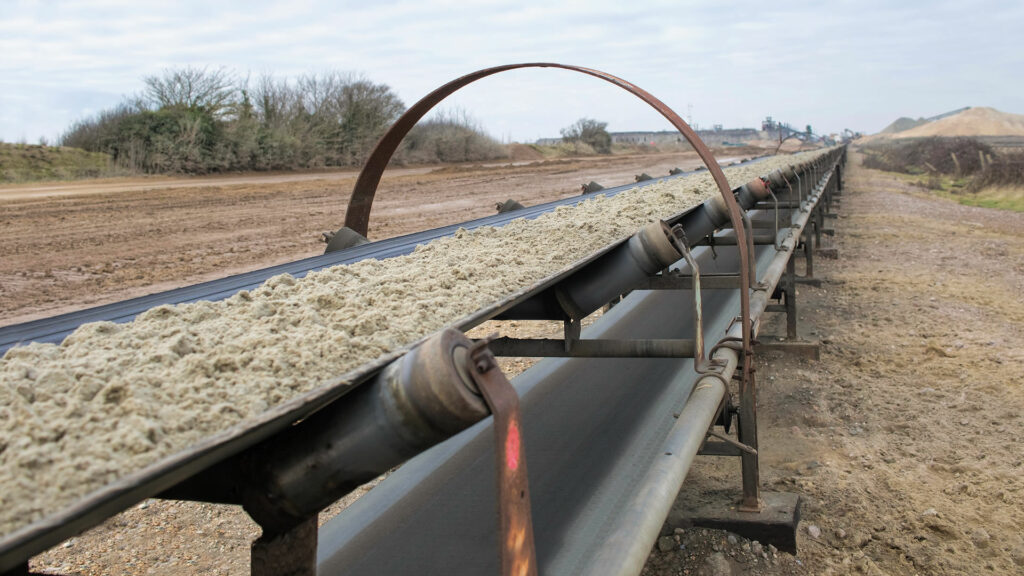
A menudo atribuida al científico Albert Einstein, la frase “Dios está en los detalles” es una interpretación de un conocido pasaje de la Biblia hebrea, el Parashá Mishpatim. La frase ilustra perfectamente cómo un detalle puede, por ejemplo, ser fundamental para separar el éxito y el fracaso de un proyecto.
En el caso que vamos a presentar hoy, los rodillos fueron fundamentales para definir el éxito o el fracaso de este proyecto.
En 2017, Fospar, la única industria de fertilizantes fosfatados del estado de Paraná, contactó a Mercurio para fabricar un correa transportadora para reemplazar la correa que estaba en operación.
Ubicada en la ciudad de Paranaguá, con terminal portuario propio en el puerto de la ciudad, uno de los más importantes de Brasil, Fospar representa alrededor del 10% de la producción nacional de este importante insumo agrícola.
Consciente de la responsabilidad del emprendimiento de fabricar una correa capaz de transportar superfosfato simple – un tipo de fertilizante que alcanza una temperatura de 150º C -, Mercurio entregó al cliente, en septiembre de 2017, la correa transportadora modelo CT ABT 4PN 2200 80” x 105m.
“Según nuestra experiencia, era el modelo ideal para trabajar durante el período de 12 meses, de acuerdo con las expectativas del cliente”, recuerda Oséias Neves Boaventura, responsable del servicio comercial del cliente, que en ese momento trabajaba en Ingeniería y Asistencia Técnica de Mercurio.
Sorprendentemente, unos 3 meses después de su instalación, se le informó a Oseas que la correa presentaba un gran desgaste localizado. Una historia que también había ocurrido con cinturones anteriores de otros fabricantes.
“Cuando nos dimos cuenta del problema, la impresión fue que esa correa no iba a poder operar durante el tiempo programado y contactamos a Mercurio”, afirma Jorge Stachoviak, Encargado de Depósito de Fospar.
Entender el caso
Dada la urgencia de la situación, Oséias programó una serie de visitas técnicas mensuales, la primera de las cuales se realizó a principios de diciembre de 2017. “En Fospar pude observar que la correa presentaba grietas superficiales, que son normales, debido a los picos de temperatura que se dan durante el proceso. Sin embargo, aparecieron de manera precoz líneas de fatiga en los techos inferior y superior”, recuerda.
Las líneas de fatiga, explica Boaventura, son marcas de desgaste más profundas que deforman la correa, comprometiendo su funcionamiento. En algunos casos, estas marcas acaban dejando al descubierto la carcasa provocando un contacto directo con el material transportado.
Gracias a la experiencia adquirida en años de trabajo en el área de Ingeniería y Asistencia Técnica, en la primera visita, Oséias pudo identificar la causa del desgaste prematuro de la correa: la misma que provocaba el gran daño en las correas anteriores.
“Después de hacer analizado bastante, me di cuenta de que el problema no era la correa en sí, sino algunos otros componentes del equipo que no estaban funcionando de acuerdo con lo deseado. Más específicamente, el posicionamiento del rodillo central del soporte de carga”, cuenta.
Rodillos de correa transportadora: Milímetros de marcan la diferencia
Los rodillos son piezas fundamentales para el perfecto funcionamiento de la correa, previniendo o retardando la aparición de líneas de fatiga. Sin embargo, un desnivel de unos 50 milímetros en los caballetes estaba provocando que el rodillo central, precisamente el encargado de evitar la aparición prematura de líneas de fatiga, presionara la correa, provocando la aparición de estas líneas y una doble deformación.
La condición se agravaba aún más por las altas temperaturas de la carga transportada, que naturalmente endurece, envejece y vulcaniza el caucho de la correa.
“Con el caucho más rígido, pierde su propiedad mecánica y su elasticidad. Esa condición, sumada a la situación atípica en el equipo, generaba una acción mecánica, perturbando su normal funcionamiento, acelerando el desgaste, grietas y roturas en la correa”, explica Oséias.
Para corregir esta situación, se sugirió un cambio en la estructura de los soportes de carga.
Siguiendo las indicaciones técnicas, el cliente elevó la altura del rodillo central, sin necesitar cambiarlo.
Según Oséias, “la orientación fue elevar el rodillo central 50 milímetros para eliminar el contacto con la esquina de los rodillos laterales. Entonces los rodillos quedarían nivelados y la correa pasaría por encima de ellos, sin contacto con la esquina del rodillo”.
Una desviación de 5 centímetros fue la causa de la fatiga que estaba dañando prematuramente la correa transportadora.
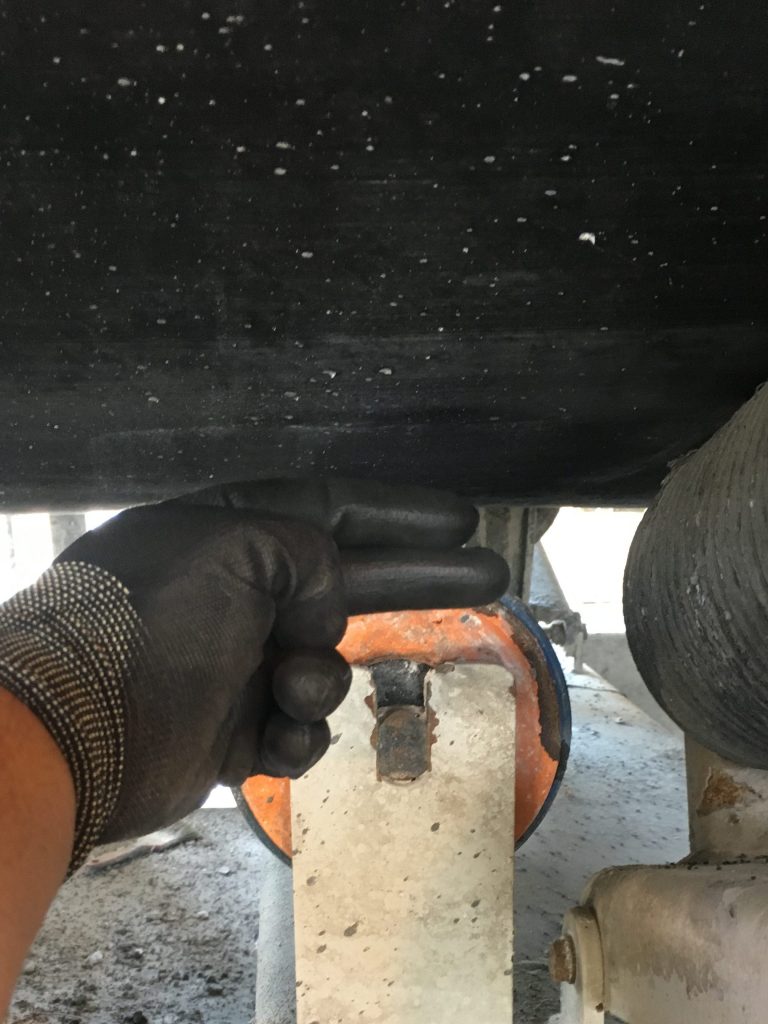
El diagnóstico preciso cambió por completo el escenario.
“Son los detalles los que marcan toda la diferencia. Con la experiencia, aprendimos que la correa ‘nos dice’ lo que le está pasando. Tenemos que estar atentos para saber interpretar y hacer el diagnóstico correcto”, enseña Oséias.
La calidad y la confiabilidad no se negocian
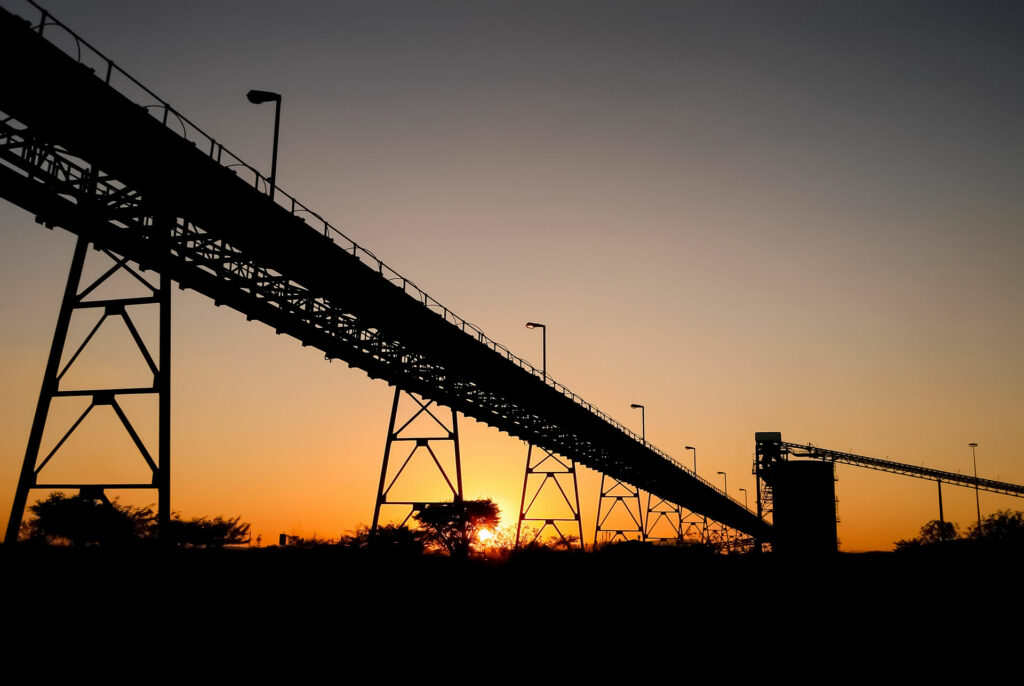
Como resultado, el ajuste en la estructura de los soportes, además de evitar el reemplazo de la correa transportadora, garantizó su vida útil por 17 meses, es decir, 5 meses más que la previsión inicial.
“El seguimiento mensual fue fundamental no solo para ajustar el funcionamiento de la correa, sino también para prolongar su vida útil. El conocimiento y la experiencia de Mercurio nos dieron toda la seguridad para postergar el cambio de la correa”, enfatiza Stachoviak.
En febrero de 2019, Mercurio llevó a cabo el remplazo de la correa en Fospar. Con el ajuste realizado en los soportes, la previsión inicial es que la nueva correa pueda operar durante 2 años, sin sorpresas y con total seguridad.
Vea a continuación el antes y el después de la alineación de la correa.
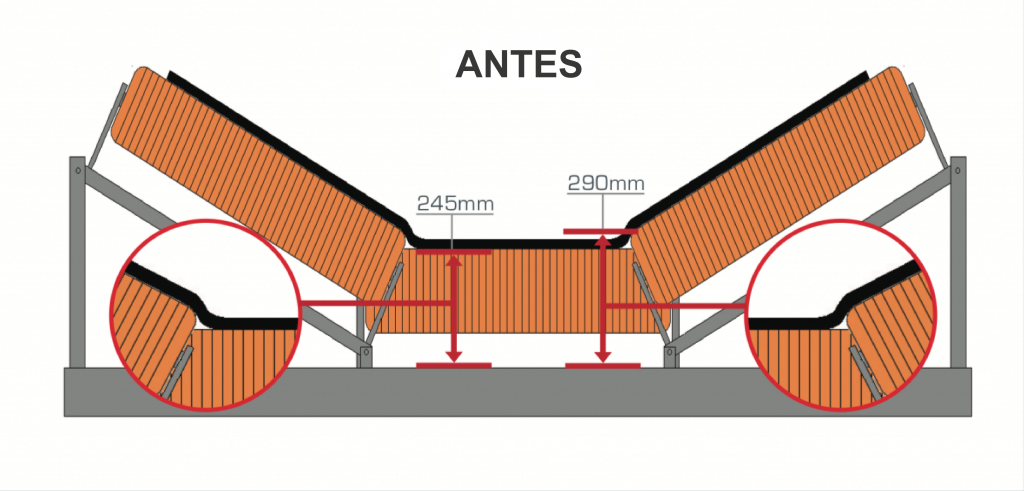
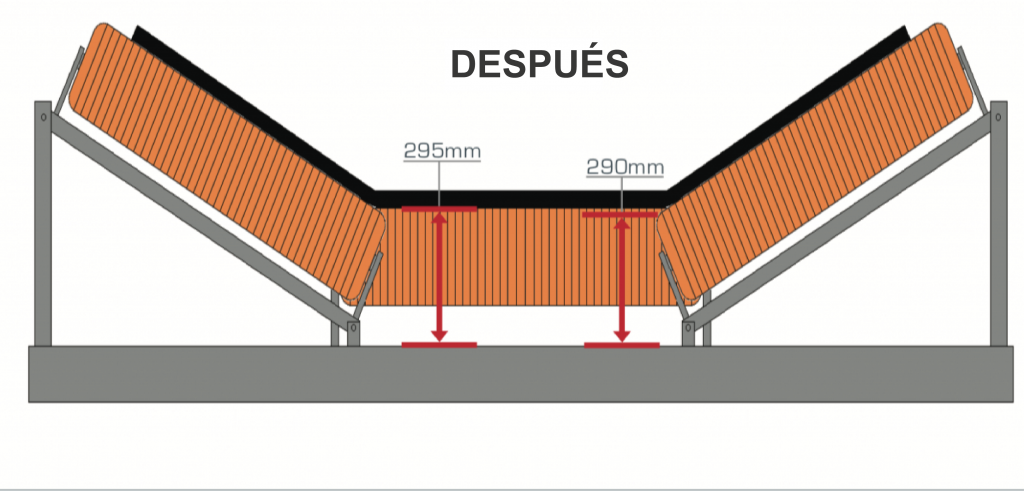