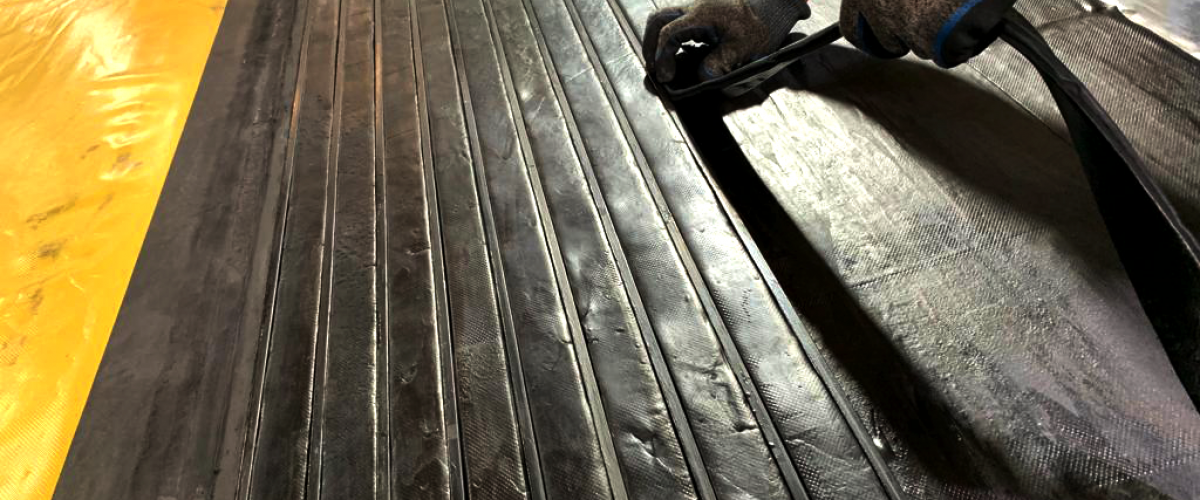
Conveyor belts are present in several segments and have a very important mission: to transport various types of materials and help move the world economy.
These devices help move production while offering savings per unit transported, safety, efficiency, agility in tasks, and operational reliability.
In order for this to be reached, procedures such as splices are essential. Because of that we have prepared this content with plenty of information about conveyor belt splicing. Keep following us and enjoy your reading!
What is a conveyor belt splice?
First, it is necessary to understand that a conveyor belt is a piece of equipment used to transport or move solid bulk materials in high volumes continuously over pulleys and idlers. The conveyor belt is the main item of a conveyor system.
So, in short, a conveyor belt splice is the joining of the two ends of a conveyor belt.
It is essential that this procedure be done efficiently by experts to ensure more safety, reliability, and agility in operations and thus avoid possible breaks and interruptions of the production process.
After all, it is an essential component for moving various materials used in industries in various sectors of the economy, especially mining.
In addition, it is important to note that conveyor belt splices are done on both fabric and steel cord conveyor belts.
How splices are done on conveyor belts?
Splices on conveyor belts can be performed in three ways: mechanical (using staples), hot (vulcanized), and cold (self-vulcanizing).
When choosing the type of splice, the materials to be transported and the characteristics of the conveyor belt are taken into account.
So keep reading to better understand each model!
Cold splice
Cold splices on conveyor belts are done when the two parts are joined by using chemicals such as an adhesive and a catalyst along with special tools such as a pressure roller, pliers, a metal ruler, and a square.
This process helps the equipment downtime to be reduced, thus avoiding high costs and financial losses for the company.
Hot vulcanized splice
Hot splices on conveyor belts are done by using a vulcanizing press that uses heat for joining the two parts of the belt.
It is also important to point out that the first procedure for carrying out a splice is calculating its length, which will depend on the method to be used. All splices should be done at an angle to reduce the effects of the belt’s flexibility on the pulleys and passing through the scrapers.
Mechanical Splice
This type of conveyor belt splice uses special staples or fasteners that can be made of steel, carbon, or stainless steel, so the joining occurs from a mechanical stapling system of the ends by using a hammer or an electric riveting machine.
Usually mechanical splicing is chosen for belts located in humid, very dirty environments or in emergencies.
The importance of expertise support during the splicing process
Technical support from those who know about conveyor belts well is essential to make sure that the splices are done according to the specifications and targets set.
There are several benefits when relying on this type of expert, such as:
- Ensuring the quality of the execution: technical support can identify problems during the execution and make sure that solutions are implemented before they cause significant impacts;
- Meeting deadlines: technical support can monitor the progress of the execution and ensure that the work is completed on schedule;
- Making sure all resources all avaible: technical support can help make sure that the resources necessary for carrying out the splice are available and used efficiently. No overspending, especially when there is a need to correct erroneously executed projects.
In short, technical support is crucial to ensure the quality, efficiency, and effectiveness when carrying out splices.
Advantages of splices in conveyor belts
Splices are essential for several operations, especially when it comes to Long-Distance Conveyor Belts where there is a need to join different belts before they even go into operation. After all, due to their weight and size, it is impossible to transport them already assembled.
So one of the main advantages of splices on conveyor belts is operational optimization.
A big advantage of splices on conveyor belts is to ensure their operation because when there is a problem, instead of replacing the entire belt with a worn or ripped part, the splice makes it possible to change only the damaged section.
Splicing also reduces maintenance time and replacement cost.
Frequent problems with conveyor belt splices
Although splices are an effective solution for damaged or worn belts, when done incorrectly, they can present problems. One of the most common is the rupture of the conveyor belt during its operation, thus causing the production line to stop completely. It is also common for the two ends of the belt to not be glued well and come apart, which can lead to interruptions in the transport of materials. It can also increase the risk of the belt breaking.
About 40% of the technical assistance requests we receive from our customers and other companies in this market are about splicing issues.
So, what are the main causes of splices rupturing?
Essentially, ruptures can occur due to cracks, cuts, or blisters in areas that have been spliced. Watch the video we have prepared with the most frequent situations:
Mercurio Conveyor Belt: You can count on our conveyor belt specialists for your splicing projects.
As you have seen, the splicing of conveyor belts is necessary for a number of reasons such as extending the belt’s service life and minimizing transportation breakdowns, but there are several factors that could damage the equipment and require repairs, such as:
- A crack in the splice closure;
- A cut in the plies;
- A rupture in the textile filaments;
- Splice misalignment;
- Incorrect measurement and control of the dew point on the splice’s surface;
- Too much adhesive applied to the splice;
- A splice kit was used that is incompatible or out of validity;
- And others.
So to do splicing on your conveyor belts, it is necessary to rely on the support of professionals who know the processes well, understand how the material is manufactured, and even its maintenance after it is already in operation.
Our technical team is highly qualified to meet the support needs of your operation’s splicing projects. Get in touch with our experts and receive access to tailor-made solutions for your company!
And to keep getting more tips on the correct transportation of materials, continue on the Mercurio Conveyor Belt Blog!