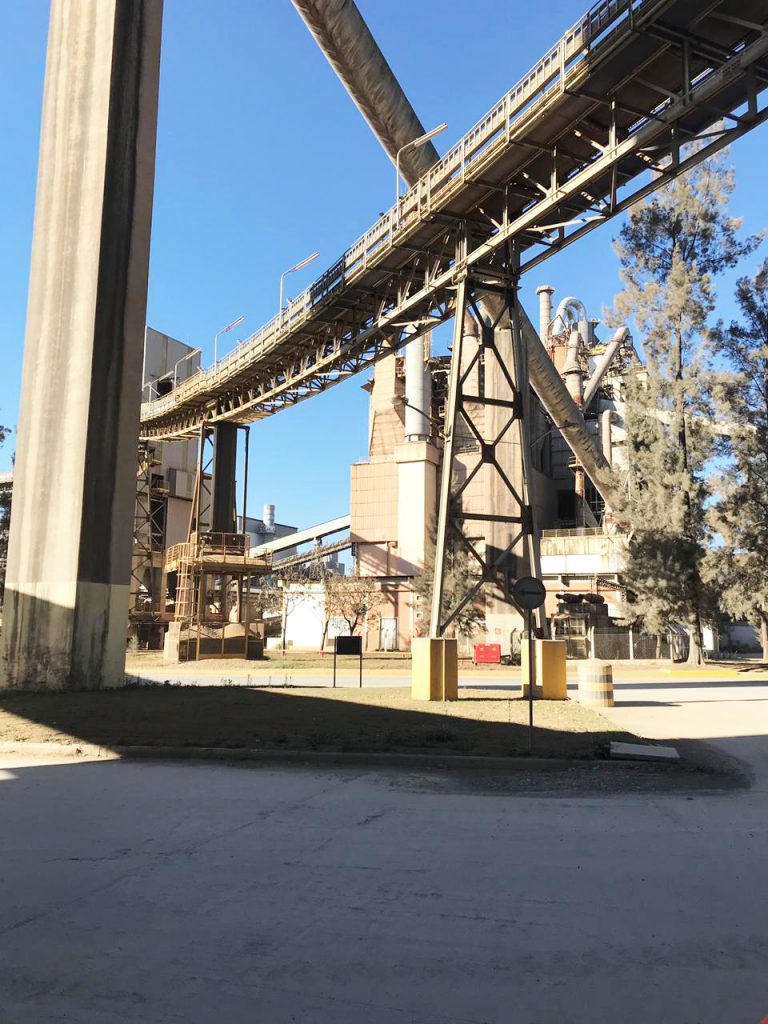
External view of the LafargeHolcim Barroso Unit.
As the saying goes, “Where there’s a will, there’s a way.” It was with that thought that Mercúrio’s team was able with great commitment to bring to fruition another success case for the company: provide an important Pipe Conveyor Belt for LafargeHolcim to generate higher productivity and lower expenses for this customer, thereby consolidating the partnership and strengthening mutual trust.
LafargeHolcim is a world leader in providing construction materials and solutions across the globe. The company operates one of the largest producers of cement and aggregates in Brazil in the city of Barroso, Minas Gerais.
“After several visits to the plant for presenting Mercurio‘s advantages and showing how much we could add to the business, we managed to prepare a report detailing the failures and anomalies of a conveyor belt manufactured by a competitor,” recalls Ivo Genelhu de Souza who was the person at Mercurio responsible for giving support to this customer at the time.
And it was not just any conveyor belt, but the first pipe conveyor belt for transporting cement in Brazil, responsible for carrying the cement from the mill to the silos. That means its importance is enormous for the plant’s operation and its downtime results in the entire operation shutting down, generating many losses for the customer.
According to LafargeHolcim‘s June 2019 report, the belt of over 700 meters long was showing strong signs of wear with several cracks. Under these conditions, the belt, which was designed for a useful life of approximately 4 years, needed to undergo recurrent changes along about 30% of its body every 2 years, in addition to being designed with 4 splices that presented critical problems, threatening to rip at any time.
Considering this scenario, Mercurio Conveyor Belt’s task was quite challenging: significantly increase useful life, reduce customer costs with splices, along with consistently tracking the belt’s performance with periodic reports.
Fiel study to develop the best solution
After analyzing the report sent by the company, Mercurio made visits to the plant to inspect the operation and after running some analyses, its Technical Sales teams put together a diagnosis that included solutions suggested, supply deadlines, installation, and costs.
“During one of these visits made together with our Technical Advisor at the time Ivan Vitor de Souza, we carried out an even more detailed inspection and analyzed the product in our lab in Jundiaí,” recalls Ivo.
Another important piece of information investigated by Mercurio was the type of material being carried. Cement leaves the mill and comes in contact with the belt at an average temperature of 100°C. The belt deteriorates faster when exposed to high temperatures.
Diagnoses and results for deploying a pipe conveyor belt
With all the necessary information, the team presented a definitive diagnosis to LafargeHolcim’s Planning Supervisor, Victor Luiz Pereira de Moura, and to its Corporate Manager, João Amaral: the belt’s brittleness, its longitudinal cracks across the entire length and on the splices were being caused by the high temperature of the cement being transported.
The following solution was presented to solve this issue: a pipe conveyor belt with a High Temperature (AT) cover should replace the competitor’s Extra Abrasion (EA) cover. “The EA cover specification withstands a maximum temperature of 80°C, while the AT in our portfolio is ideal for transporting more abrasive materials and can withstand much higher temperatures, such as the cement being carried by this belt,” he explains.
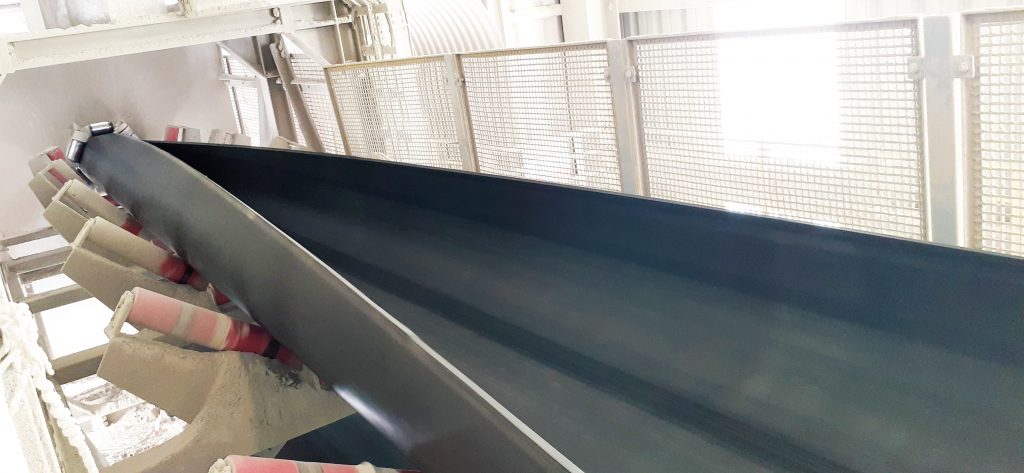
In addition to the change in specification, Mercurio also suggested to increase the thickness of the upper cover, further reinforcing its protection against the actions of the material carried over time.
For even greater durability, another modification was suggested, which was to reduce the number of splices from four to one, which not only prevents cracking, but decreasing the amount of splices represents a significant reduction in operating and labor costs for the customer.
With all these adjustments, the conveyor belt designed and supplied by Mercurio would have a life expectancy of 6 years compared to the 4 years of the previous belt, a 50% increase. Furthermore, with the changes suggested, changing 30% of the belt every 2 years would no longer be necessary. Another important advantage was to decrease the number of downtimes for splicing changes, ensuring greater productivity for the plant.
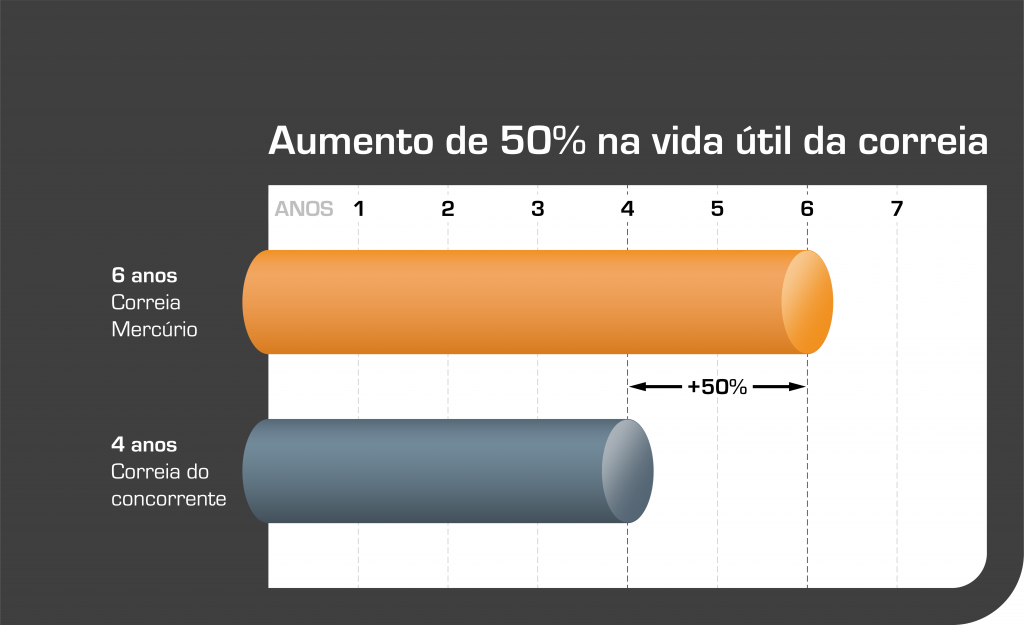
Comparative: Mercurio Pipe Conveyor Belt vs. competitor
Amazing results and satisfaction guaranteed
Once the full report was presented with all the advantages, benefits, and performance expectations, LafargeHolcim installed the pipe conveyor belt supplied by Mercurio in January 2020, replacing the problematic belt.
Since then the belt’s performance has been successfully meeting all expectations presented.
“The technical studies presented in several reports we prepared demonstrate the excellent performance. We are very pleased with the first results and optimistic about increasing productivity and reducing costs at the plant,” celebrates Victor Luiz, Supervisor at the LafargeHolcim Barroso Unit.
These results have been confirmed through periodic visits made by Ivo together with Mercurio’s technical team. “Every 60 days on average we perform detailed inspections for monitoring performance through measuring hardness, temperature, and other relevant information that is updated in detailed reports sent to the customer”, reinforces Ivo.
“We are very pleased not only with the solution presented by Mercurio, but mainly with the level of involvement of its entire team. The customer service provided during the process since the first visits, all the way up to installation follow-up, and now with the periodic visits to check the belt’s performance leaves us much more confident and proves that we made the right decision”, attests Victor.
This success case opened doors for Mercurio Conveyor Belt in new projects with LafargeHolcim such as other belt supplies to the Barroso plant and another belt for the Pedro Leopoldo plant, also in Minas Gerais.
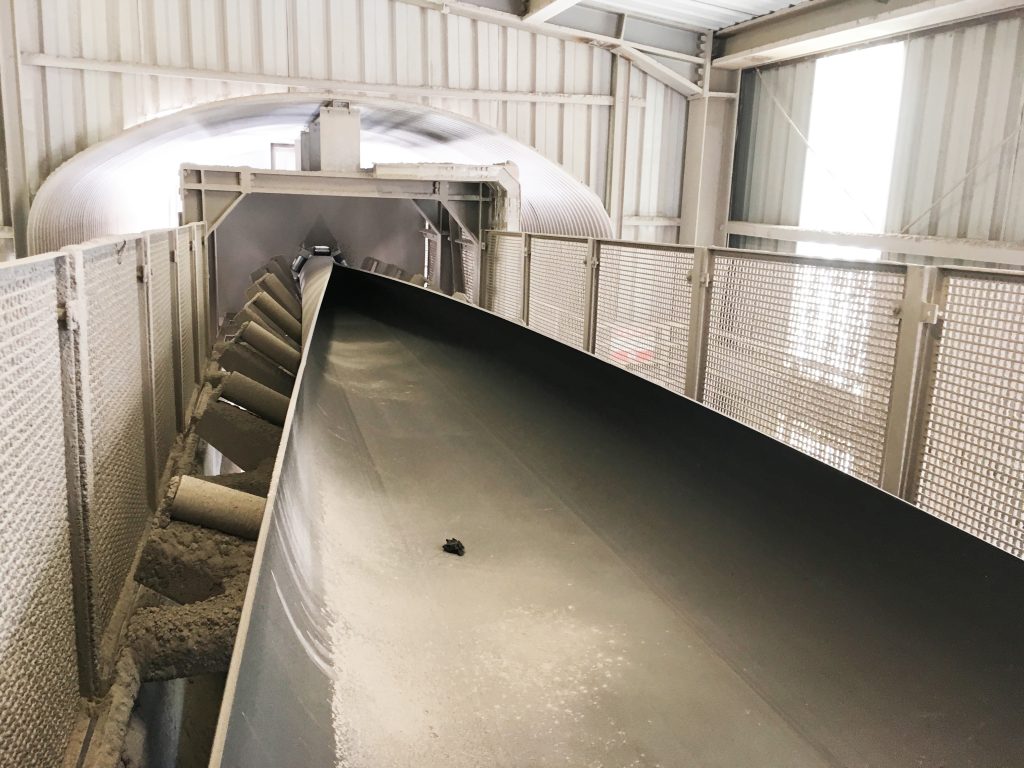
With a High Temperature (AT) cover, increased cover thickness, and less number of splices, Mercurio’s Pipe Conveyor Belt has a life expectancy of 6 years and a significant decrease in downtimes.