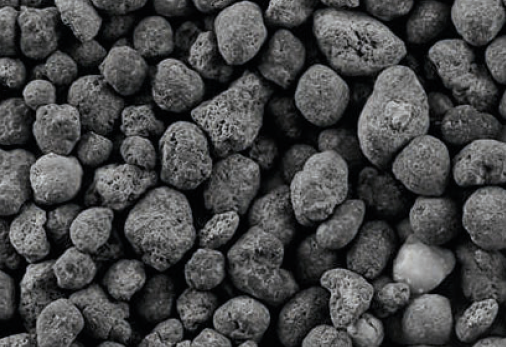
An important global agribusiness industry with more than 15,000 employees and operations in more than 160 countries, Yara Brasil sought out Mercurio Conveyor Belt with a very specific objective: solve the problem of an important conveyor belt.
Responsible for moving the production at Yara’s RIG1 Plant located in the city of Rio Grande, Rio Grande do Sul, the conveyor belt of this equipment would always get worn out within a short period of time, forcing the customer to carry out four to five changes a year.
“We have some dosing belts that required recurrent changes. The company would install a belt and after two or three months it already had to change it again. After carrying out some technical inspections, I decided to contact Mercurio Conveyor Belt in search of a solution to our problem,” says Manoel Cosme, the Unit’s Equipment Inspector at the time.
Faced with this challenge that caused a serious bottleneck in production besides constant expenses, Mercurio Conveyor Belt was contacted to help find the best solution for the case and Oséias Neves Boaventura, who was responsible for providing Sales Support to Yara, came to the rescue. He was taking the initial step in a partnership that would soon yield excellent results.
Mercurio conveyor belt diagnostics
When analyzing the scenario, decisive factors were observed that could cause a rapid wear of the conveyor belts.
First was the type of material being transported, a high-abrasion phosphate fertilizers. Also, because they are dosing belts, they work at a low speed and also have a high impact from the Feeding Chute, which is an integral part of the conveyor system that has the purpose of receiving the material transported and directing it correctly to the conveyor belt.
All these characteristics combined resulted in a great deal of damage to the belt.
With this information in hand, the need for a conveyor belt of a new specification with a much more reinforced cover was discerned. “Our suggestion was to replace the belt with one from Mercurio with an XEAS (Extra Abrasion Super) cover, which is certainly more suitable for high abrasive situations as the one in this case,” Oséias recalls.
It was also suggested to increase the belt’s thickness from 3/16” to 1/4” in the upper cover and from 1/16” to 1/8” in the lower cover.
With the new specifications, the initial objective was to double the belt life, so instead of four annual changes on average, the customer would begin changing the belt only twice a year, which would already result in a great improvement.
Conveyor belts installed and operating
The suggestion was readily accepted by Yara. “One week before the date agreed to change and start working with the new belt, at the end of May 2019, the belt in operation ruptured, which anticipated needing to install Mercurio‘s new belt, and we began to track its performance,” recalls Cosme.
After that, visits were scheduled every 2 months between Oséias and the Mercurio Conveyor Belt team together with the customer for monitoring the performance of the new belt.
Improvements could already be seen in the first inspection. For example, unlike the previous belt that within these two months already showed strong signs of deterioration with wear and even apparent rips, the new belt was practically intact, demonstrating that it would pass the test, being able to complete the initially scheduled period of 6 months with flying colors.
Belt life 12 times longer
The positive impact of the new investment was quickly noticed because not only were there savings with less conveyor belt changes, but there was also a decrease in the number of downtimes in the production park required for each change, substantially increasing the operation’s performance.
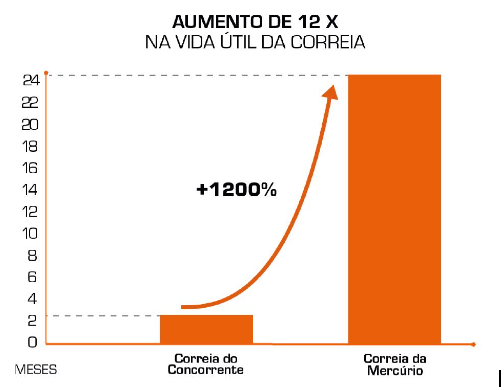
Only a company with a team of specialists in conveyor belts recognized by the market and with a deep knowledge of the implications for the application can offer this level of service.
Thanks to the initial good performance, the customer started to order other belts for the Yara Rio Grande Unit and within a short time, Mercurio’s conveyor belts with a special cover and high abrasion resistance began to be installed throughout the plant.
“Expansion was inevitable. We are talking about feeding belts that if they break, the entire production stops,” explains Cosme. According to him, the Rio Grande Unit has approximately 20 kilometers of conveyor belts. Of this total, most are already provided by Mercurio Conveyor Belt. “In just 8 months we took on the delivery of about 100 belts to the customer. This is an excellent result that proves the success of this new partnership,” celebrates Oséias.
Currently the belts supplied by Mercurio are already in operation not only in the RIG1 Unit, but also in its new plant in the granulation sector and on the unloading pier.
Yara fertilizers and Mercurio conveyor belt: a partnership beyond business
Also due to Manoel Cosme’s initiative, who has already been promoted to Unit Maintenance Superintendent, a Workshop was held in August 2019 on the “Best Practices in Conveyor Belt Operation and Maintenance” with support from Mercurio Conveyor Belt.
The event had the objective of bringing the various manufacturers together with the employees from the areas of operation, maintenance, warehouse, inspection, and scheduling to show the care that should be taken on a daily basis in addition to presenting products, services, and solutions available on the market in order to ensure the best performance of the equipment’s operation,
an action considered strategic to ensure the best operation and results of the plant’s conveyor belts.
At this time, Mercurio shared its expertise and best practices for belt inspection and maintenance and later the information shared during the event became a reference for other units in the company.
While new projects between Mercurio and Yara Brazil are already underway, the belt installed in May 2019 with the initial life expectancy of 6 months continues to work at full steam. According to the follow-up carried out by both companies, the forecast was updated to a useful life of two years—so 24 months! An indisputable demonstration of accuracy and precision in the specifications and changes suggested by Mercurio and adopted by Yara.
The after-sales support and technical follow-up presented by the Mercurio team are also highlighted as being fundamental in this success case, according to Cosme, which comes
from someone who knows the matter deeply. “I say that conveyor belts have been a part of my life since I was born. My father, known as ‘Mr. Newton´, started working with conveyor belts in 1974. He has kept up his belt maintenance company until today. In other words, it is something that is in our blood. That is why I know about the importance of making the right investments in the best equipment and to have partners really committed to excellent results,” he concludes.