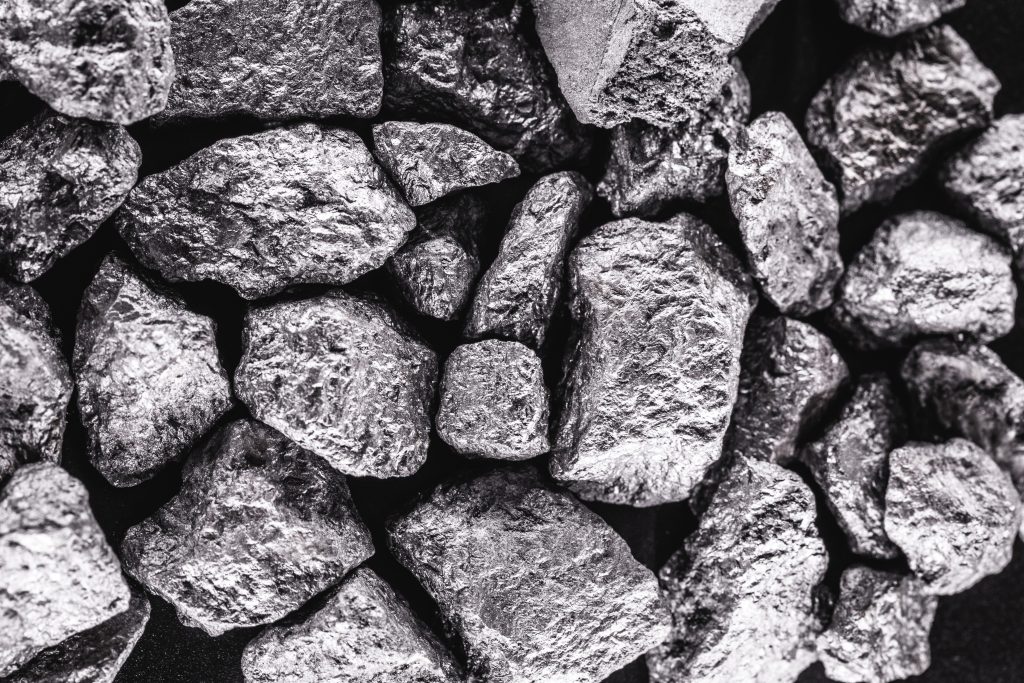
Niobium is a raw material that brings high resistance to metallic alloys. Its name refers to the story of Queen Níobe who was transformed into a rock by Zeus, according to Greek mythology.
The ore is widely used in the automotive, naval, petrochemical, and infrastructure industries and is used to manufacturer long pipes, hot-rolled laminates for manufacturing cars and cold laminates, used in large building projects, among other uses.
Brazil is the world’s leading producer of niobium, responsible for about 75% of the world’s production of this ore, and much of this total is extracted from the Boa Vista mine located in the city of Catalão in Goiás.
The company is part of a Chinese group and is the world’s second largest producer of niobium in the world and has been a Mercurio customer for about 20 years.
“We have a solid relationship built thanks to a partnership that values superb services and commitment to the customer’s performance,” explains David William Souza, Account Manager at Mercurio.
In his role, Souza makes periodic visits to the customer with the objective of identifying new opportunities, functionalities, process improvements, or also to propose new technologies within the conveyor belt market.
It was on one of these routine visits to the giant niobium producer in the second half of 2017 that the opportunity arose to propose an improvement.
The company’s engineer came to tell us about a problem on a drag feed conveyor belt that was showing very low service life. On average it needed to be changed every 45 days, he recalls.
Ore Conveyor Belts require more resistance to cuts and tears
Conveyor belts with a drag feed require specific qualities in order to withstand a high quantity of material and impact.
The belt receives all the weight from the load deposited by the Feeding Chute, which is an integral part of the conveyor that has the purpose of receiving the material transported and directing it correctly over the belt, literally dragging that load on it.
Working loaded, the chute decreases the high impact of the load on the conveyor belt, but it requires more effort to perform the “drag”.
“The previous belt had an Extra Abrasion (EA) cover, which is a type of rubber with good abrasion and wear resistance, but it is a cover that does not do so well in situations where there is cutting and perforating caused by the impact of the material,” recalls Souza.
“On the day of the visit, we noticed that the belt had typical high impact wear,” he recalls.
From this situation, the Mercurio team went home with a new challenge: propose an improvement in the belt that would have the same abrasion resistance as the EA cover, but that also had resistance to impact and tear,
Changes that made the difference
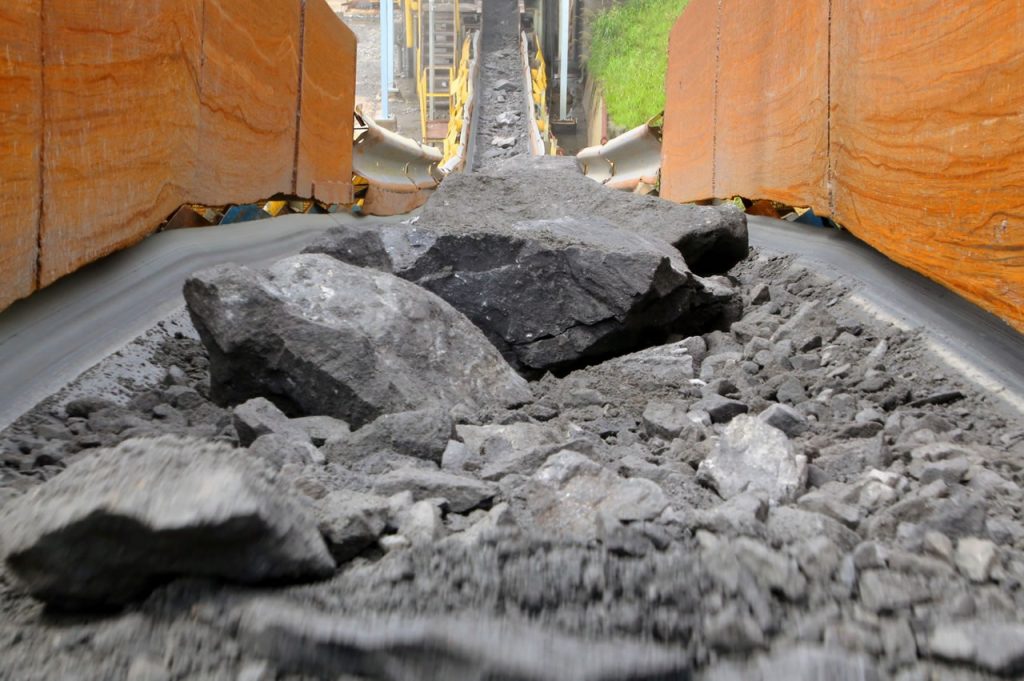
Thus, the first measure taken by Mercurio‘s technical team was to change the specification from an EA cover to MercoRip, a type of compound that has superior characteristics to EA rubber, providing greater absorption to impact and resistance to tearing.
Next, a second measure was adopted to fulfill another request.
According to the customer, the belt also suffered from cuts and tears generated by the loading and characteristic of the material: “Sometimes the ore arrives contaminated with rebars, pieces of iron, among other cutting materials, not to mention that niobium is a very hard and dense ore that sometimes comes in lamellar rocks with sharp edges that end up wearing down and cutting the belt”, he explains.
In this case, Mercurio‘s technicians chose to include a Rip Proof aramid mesh that allows for greater absorption and distribution of the impact, preserving the carcass.
Twice the service life and annual savings of 30%
After these changes were made to the belt’s specifications, Mercurio‘s team continued to follow up on the performance and the result was extremely positive.
“Within a short time we noticed that the change in the cover to a MercoRip and the inclusion of the Rip Proof aramid mesh was really quite assertive. We managed to double the belt’s service life, going from 45 to approximately 90 days,” celebrates Souza.
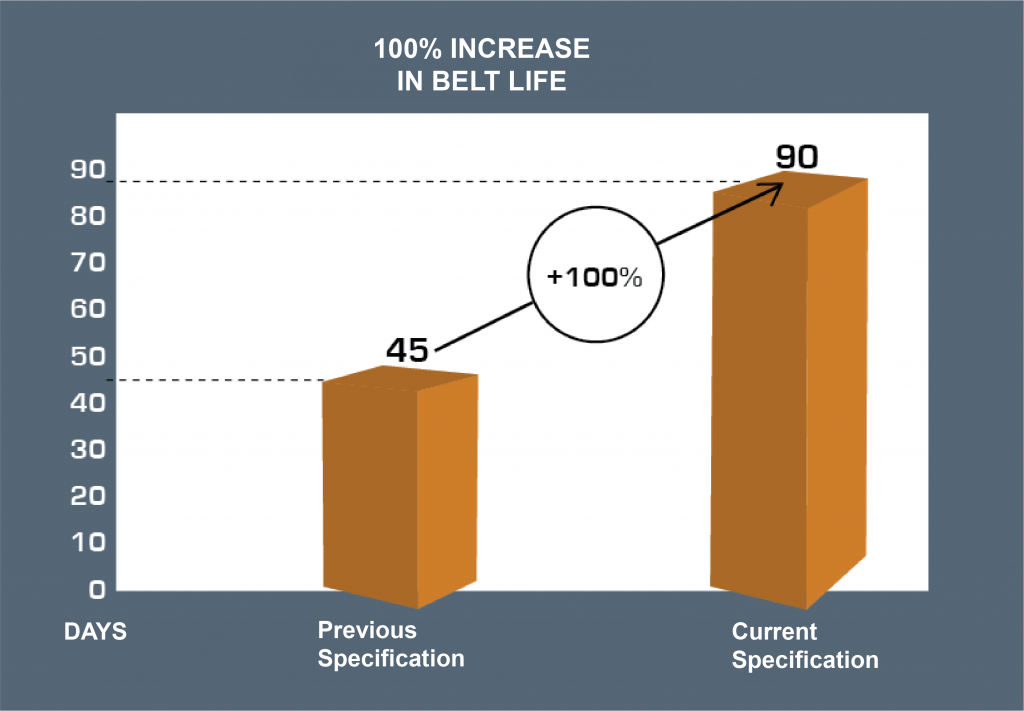
Taking into account the 100% increase in belt life, the decrease from eight to four downtimes for changes per year, the lower number of splices made, and consequently the decrease in labor cost, Mercurio’s team estimates that the change in the belt design represented an annual savings of about 30% for the customer. All that means greater productivity, reduced downtimes and expenses, with product reliability.
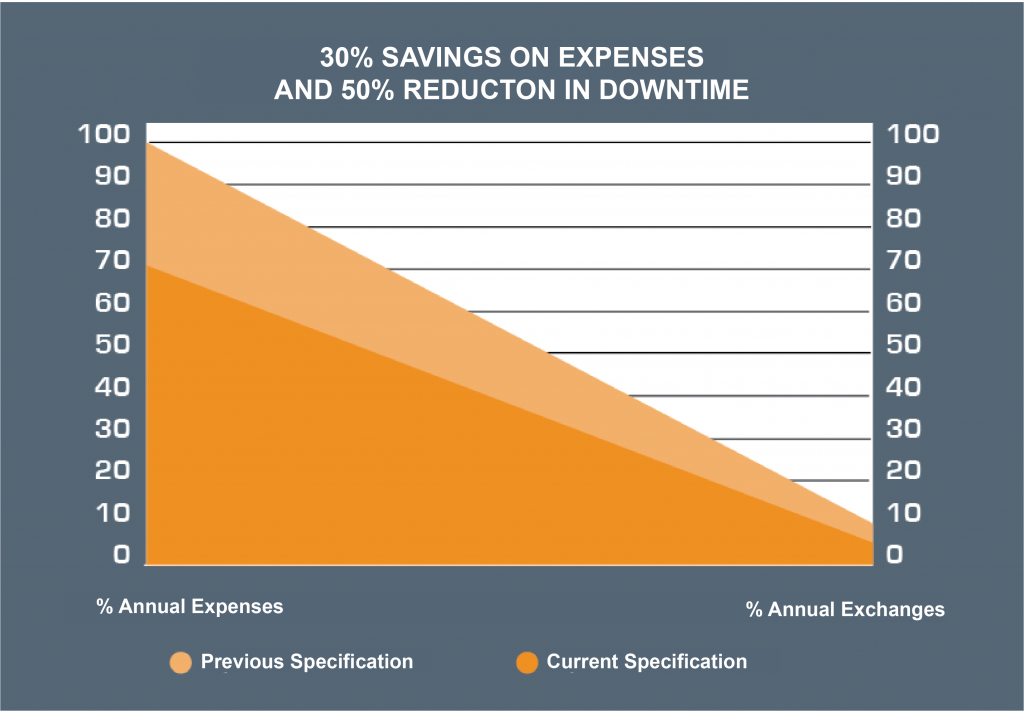